Imagine you had a great idea for new technology that could efficiently heat and cool a building with less pollution, energy, and cost than most existing systems…
That’s great! So how much will it cost for me to install it? How much energy can I get from it? How big of a system do I need for my home? What about for this other project in a completely different location and climate?
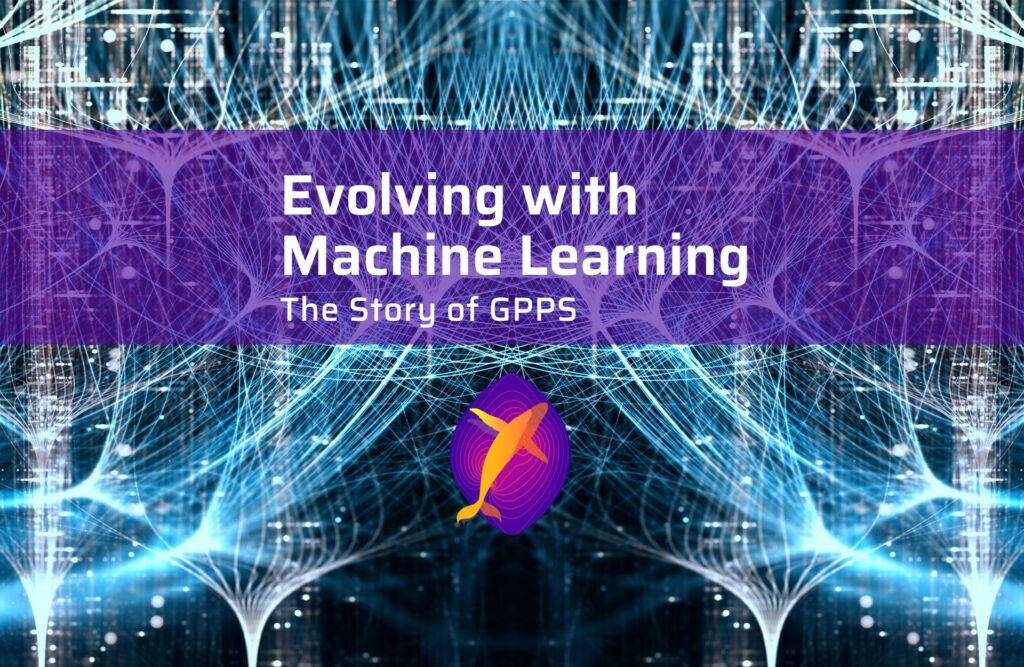
These are the questions that one of our clients at Umny needed help answering. They had a brilliant idea for a new system that uses building foundation equipment (called “piles”) to generate heating in the winter and cooling in the summer. This type of underground geoexchange system is becoming more and more popular around the world, and it has a lot of promise to address our global energy needs.
But they faced a major (and common) problem: how do they choose the right size of system to make sure they supply the energy that their customers needed? How many piles would they need to install?
Drilling is a lot harder than it might look. The costs of getting highly-skilled people to come in with specialized equipment to drill through the surface of the earth – while adjusting for different conditions in every location – can be massive. This is one of the main reasons that geothermal energy is still so costly compared to above-ground renewable systems that use air, sun, or bodies of water.

This also means that it’s very hard to test out a new invention – and to find out what the ground conditions are in a new area.
Phase 1: Rules-of-thumb
To deal with this, we often have to rely on rules-of-thumb and general guidelines – this is what the industry was doing when we first met our client. Without being able to experimentally test this technology, many designers will build a system with a practical guess of how it should be, and then find out later if it works or not. These guesses may be informed by the expert experience of drillers who’ve been building these systems for years, and they often also include some manual physics calculations. However, the ground is too unpredictable to rely on these standards alone, so the best way to do this is to seriously oversize the design just to be safe.
These systems end up trading accuracy for cost. This means they have to drill more and more expensive holes (using a large “factor of safety”), to make up for any errors because of the assumptions in the design. The Canadian GeoExchange Coalition found that some projects are being oversized by more than 150%!

Unfortunately, even if these systems are oversized, they can still fail to meet the building’s needs or protect the ground’s natural energy. We’ve heard of some geoexchange projects that overheat their ground so much (by putting in more heat than the ground can balance) that they were solidifying the clay beneath them. These systems were actually baking the ground they were built in, and the owners had to install other expensive cooling equipment just to try and save their soil.
Our client understood this problem, and needed our help to solve it. Our challenge was to test out and optimize new designs – but without having to physically build them, or rely on common assumptions that could lead to their failure.
Phase 2: Computer Simulation
This led me to work with computer simulations. I created virtual models of this technology so that we could iterate without the cost of real-world trial and error. I spent a couple years optimizing the design, and adding more detail to the ground to increase our accuracy and avoid the problems faced by others in this field. You can read some of these findings in my publications.

This method, sometimes referred to as Numerical Modeling, Finite Element Analysis, or Computational Fluid Dynamics (CFD), has created a big leap in the industry. Many designers these days will hire someone to run these simulations when creating a new project.
We can use these models to find out:
- the depth and size of in-ground heat exchanger pipes,
- how many pipes should be installed,
- what speed the fluid should be pumped through them,
- and how much energy can be supplied from the ground without it overheating or overcooling.
With this new R&D tool, we pushed forward in accuracy, and this has helped to lower the cost of oversizing, or systems failing before their time.

However, doing this work through my engineering consulting positions, I realized that we still had to make a lot of critical assumptions, especially about the ground. Whenever we wanted to test something new, I had to create a new model to simulate it, then use calculations or tables that could generalize the soil properties and temperature for this site.
Even with seriously overpowered computers, these tests took a long time to run. The computer had to solve hundreds of thousands of equations for every second of time we wanted to study – and I wanted to know how this system would perform for 40 years! The quality of these models really depends on the knowledge of the person building them, and the quality of information they can feed into them. All of this costs a lot, in time and money.
So, we still faced the problem of making this new technology affordable for the users, but also for the designers.
And that challenge led us to the exciting next step in the evolution of designing energy technology.
Phase 3: Machine Learning
Pairing up with a computer programmer, and CFD expert to found Umny, we started the exciting project of training a deep learning engine to predict how our client’s system works.
We use machine learning to understand the physics of the system. With all of the knowledge we’d gained from rules-of-thumb and CFD research, we built ML models that can handle the complexity of this technology. While traditional physics calculations are limited by how complicated the system is, ML methods (such as neural networks) can look at all the variables involved to quickly understand and predict the outcome.
More information about Physics-Based Deep Learning.

And that’s how the Geo-Pile Predictive Software was born. In just a few months, we built this completely custom software for our client to understand their new technology using the power of AI.
With GPPS, it is incredible to watch tests that used to take hours or weeks, now take only seconds to run. And because these AI models learn from data, we are able to continue improving them with real-world sensor measurements from actual built projects.

Our client is enjoying the benefits of increasing accuracy in their designs, really fine-tuning their technology, and answering essential questions to start their next projects. This has been such a rewarding project; we’ve help to lower the costs to end-users and designers with this tool – making geoexchange more accessible.
Now when a developer approaches our client to ask how much energy their technology can provide in a totally new location, they can use GPPS to quickly and accurately answer that question. We even made an automatic report generator to really speed up the process of communicating the power of their technology.
Using four ML engines, GPPS can even optimize a design to reduce oversizing. It can predict performance across time, to match a building’s load profile. With our ML Ground Temperature Predictor plug-in, these studies are customized for new locations around the world, with more accurate ground information than we ever had access to before. And, unlike CFD, all of these results are generated from the same tool, without having to make a new model each time.
From starting with a rough idea for a new technology, to seeing it built in real-life, and developing its own ML software, this story has shown us a lot about the evolution of technology – and the futuristic tools we can use to build it.
At Umny, we are helping to reduce the cost of energy, by accurately modeling technology in nature. Want to know more?